Ndfeb hydrogen decrepitation.jpeg.
International Journal of Hydrogen Energy Volume 22, Issues 2–3 , February–March 1997 , Pages 241-244 Technical and operating features of interaction between hydrogens and alloys and magnets on the basis of rare earth metals
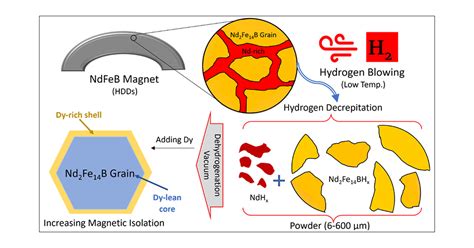
The fabrication of Nd-Fe-B sintered magnets is composed of quite a few processes mainly including strip casting, hydrogen decrepitation, jet-milling, magnetic alignment and pressing, sintering and subsequent heat treatment, machining, and surface coating. ... Possible methods of recycling NdFeB-type sintered magnets using the …Abstract. This paper reports the room temperature hydrogen decrepitation (HD) of fully dense, 2/17-type sintered magnets based on the composition, Sm (Co 0.69 Fe 0.21 Cu 0.068 Zr 0.019) 7.49. These magnets absorb significant amounts of hydrogen over an extended period (∼48 h) at room temperature and at a pressure of 10 bar to give a …NdFeB permanent magnets have different life cycles, depending on the applications: from as short as 2–3 years in consumer electronics to 20–30 years in wind turbines. The size of the magnets ranges from less than 1 g in small consumer electronics to about 1 kg in electric vehicles (EVs) and hybrid and electric vehicles (HEVs), and can be …Abstract: Hydrogen decrepitation (HD) is an effective and environmentally friendly technique for recycling of neodymium-iron-boron (NdFeB) magnets. During the HD process, the NdFeB breaks
High performance NdFeB permanent magnets are widely manufactured using the conventional powder metallurgy route involving distinct steps: alloy synthesis by strip casting, pulverization by hydrogen decrepitation and jet milling, shaping by compaction and sintering followed by annealing [32]. Every step of this manufacturing process has …The method combines hydrogen decrepitation (HD) disintegration of the initial magnet, powder sieving and the Press-Less Process (PLP), where hydride powder is sintered in a graphite mold. Coercivities up to 534 kA/m were obtained in porous samples based on powder size d < 100 µm. Adding a ball milling step resulted in full density …Over the last ten years several groups have been carrying out research into metal injection moulding (MIM) of neodymium-iron-boron (NdFeB) powders to produce isotropic or …
Hydrogen decrepitation (HD) is based on the selective synthesis of neodymium hydrides though the reaction of hydrogen gas with neodymium located in the Nd-Fe-B magnet. HD process was originally designed and patented by Harris et al. (1979) as a way to break down SmCo and Sm 2(Co,Fe,Cu,Zr) alloys. 5 17.The hydrogen treatment of the Nd‐Fe‐B alloy ingots was found to produce magnet powders with good magnetic properties. Typical magnetic properties of these powders are as follows; 4πIs = 9.5 kG, Br = 7.7 kG, iHc = 9.4 kOe, and (BH)max = 12.2 MGOe. Microstructural studies of these powders showed that they are made of fine …
Sagawa obtained ultrafine NdFeB grain by innovative HD (hydrogen-decrepitation) + HDDR (hydrogenation-disproportionation-desorption-recombination) + helium jet milling process. It should be noted that the helium gas is more suitable than nitrogen gas to fabricate ultrafine powder due to its lighter mass fraction, and will also …Anisotropic powder was prepared with precursor (NdDy)-(FeCoNbCu)-B sintered magnets by hydrogen decrepitation, desorption, and subsequent annealing treatment. The hydrogen desorption was performed in magnetic fields of 0, 1, 3, and 5 T. The orientation of tetragonal phase grains of the powder was evaluated from the …Abstract: Hydrogen decrepitation (HD) is an effective and environmentally friendly technique for recycling of neodymium-iron-boron (NdFeB) magnets. During the …The scrap sintered Nd–Fe–B magnets were recycled as the raw materials for bonded magnets using the hydrogen decrepitation (HD) process. The HD powders have the lowest oxygen and hydrogen content by hydrogenation at 150 °C with 1 bar H2 pressure and dehydrogenation at 600 °C. The powders with the largest particle size (>380 μm) …
hydrogen uptake (2043.76 μmol∙g-1) was received for conditions 4 bar and room temperature, while the lowest (925.27 μmol∙g -1 ) for 1 bar at 400 0 C (Figure 4). At room temperature (29
Sep 7, 2022 · We report investigations on the processing by Spark Plasma Sintering (SPS) of RE2Fe14B (RE = Nd, Pr…) powders obtained by hydrogen decrepitation of decommissioned magnets and the magnetic properties of the consolidated magnets. First experiments have been carried out with a commercial powder to make clear the mechanisms occurring during the powder densification. The magnetic properties of ...
The ultrafine magnet waste (particle size < 1 µm) contained around 50% rare earths mainly in the form of hydroxides as they are generated from the hydrogen decrepitation. The major phases in ultrafine NdFeB waste were Nd(OH) 3, Fe 2 O 3 and Fe phases. When ultrafine magnet waste was leached with hydrofluoric acid, all the iron …Various efforts have been made in the past for direct recycling of spent NdFeB magnet using hydrogen decrepitation followed by resintering method (Zakotnik et al., 2009; Herraiz et al., 2016). In ...Dec 20, 2020 · Extraction of NdFeB from rotors using hydrogen. Seven semi-embedded rotors and non-embedded rotors were processed separately in two experiments. All the magnets in individual slots were scored in concentric circles using an angle grinder to provide a fresh surface for the hydrogen, as shown in Fig. 3, 15–30 min before being loaded into the ... Mar 1, 2019 · Fig. 1 shows the hydrogen decrepitation curves of Nd-Fe-B SC and SM at 288 K with different initial hydrogen pressure. Under the initial hydrogen pressure of 0.1–1 Mpa, the HD process composes of four stages of magnets surface activation, slow hydrogenation of Nd-rich grain boundary phase, quick hydrogenation of Nd 2 Fe 14 B main phase grains, and slow hydrogenation of inner part of the magnets. calcium [12] and hydrogen decrepitation [1,13-19]. Many of these are under current development. Hydrogen decrepitation (HD) is based on the selective synthesis of neodymium hydrides though the reaction of hydrogen gas with neodymium located in the Nd-Fe-B magnet. HD process was originally designed and patented by Harris et al. …Permanent magnets produce magnetic fields and maintain the field even in the presence of an opposing magnetic field. They are widely used in electric machines, electronics, and medical devices. Part I reviews the conventional manufacturing processes for commercial magnets, including Nd-Fe-B, Sm-Co, alnico, and ferrite in cast and …Keywords: Finite difference method; Kinetics; Hydrogen decrepitation; NdFeB alloys; Diffusion 1. Introduction Sv (V ) expansion due to decrepitation results in a five orders of magnitude higher rate of hydrogen diffusion into The most popular recent application of hydrogen in the Nd–Fe–B alloy than into a theoretical bulk sample of that ...
May 5, 2023 · The first is the hydrogen decrepitation (HD) process, which is already used in the primary production of NdFeB magnets to convert the alloy into powder form before further comminution. 46 The second process, named HDDR, which consists of two different steps, namely hydrogenation–disproportionation (HD) and desorption–recombination (DR), was ... So exposure at LOW temperature to hydrogen leads the NdFeB pieces to react via intergranular fracturation (decrepitation), the mass of Nd2Fe14B grains forminfg a metal hydride with max ... The MMG has been active in the field of rare earth alloys and processing of permanent magnets using hydrogen for over 40 years. Originated by Professor Emeritus Rex Harris, the hydrogen decrepitation method, which is used to reduce NdFeB alloys to a powder, is now ubiquitously employed in worldwide magnet processing. Hydrogen decrepitation as a highly efficient and excellent crushing method is widely used in the preparation of NdFeB magnets. ... Expand. 1. Save. The processing and characterisation of recycled NdFeB based magnets. S. Adrwish. Materials Science, Engineering. 2013; The scrap magnets were turned into a powder using the HD process. …The hydrogen-absorbing NdFeB powder absorbs heat in the plasma and rapidly decomposes and dehydrogenates. At the same time, in the dehydrogenation process, the particles are cracked and broken to form fine NdFeB powder due to rapid heat absorption and release of a large amount of hydrogen, and the NdFeB powder is at a high …This means that NdFeB magnets are prone to galvanic corrosion, in particular, intergranular corrosion attack. The corrosion mechanism as well as the hydrogen decrepitation behaviour of microcrystalline (i.e. sintered) magnets has been studied extensively [11], [12], [13], [14].
Abstract. This paper reports the room temperature hydrogen decrepitation (HD) of fully dense, 2/17-type sintered magnets based on the composition, Sm (Co 0.69 Fe 0.21 Cu 0.068 Zr 0.019) 7.49. These magnets absorb significant amounts of hydrogen over an extended period (∼48 h) at room temperature and at a pressure of 10 bar to give a …
NdFeB-based alloys and magnets also react readily with hydrogen, and this has been exploited by the hydrogen decrepitation (HD) process [4]. During HD the material is exposed to hydrogen (at room temperature) and initially the Nd-rich phase absorbs hydrogen (represented approximately by Eq.Apr 15, 2022 · An effective and complete processing route for the recycling of sintered Nd-Fe-B scrap magnets was proposed. Sintered Nd-Fe-B magnets were subjected to the Hydrogen Decrepitation (HD) process at various temperatures in the range of 50–300 °C, at two different pressures, 50 kPa and 200 kPa, followed by vacuum dehydrogenation in the range of 720–820 °C. International Journal of Hydrogen Energy. Volume 24, Issues 2–3, 1 March 1999, Pages 257-261. Application of hydrogen vibration milling in theprocessing of NdFeB and (Nd, Pr)FeB permanent magnets. Author links open overlay panel R.S Mottram 1, V Yartys 2, P.W Guegan 1, I.r Harris 1. Show more.Jul 1, 2002 · The effective diffusivity of hydrogen in NdFeB magnets is reduced with Co and Ga additions and as a result of the texture induced in the microstructure via die-upsetting process. In addition to the results shown in Fig. 8 , the thermal desorption behaviour related to the hydrogenation of a die-upset MQU-G magnet is different for the two ... The subject of this paper is method (4) together with other aspects of the use of hydrogen in the processing of NdFeB-type magnets. 2. The hydrogen decrepitation process The manufacture of rare earth-transition metal magnets by the HD route was first proposed in a 1978 patent by Harris et al. [7].Hydrogen decrepitation process has been applied for the first time for the direct recycling of SmCo 5 magnets. Industrially produced sintered SmCo 5 magnets were decrepitated by hydrogen gas at a pressure of 1 bar to 9.5 bar at room temperature in a planetary rotating jar. After decrepitation, the starting sintered magnets were reduced to …A production-scale plant in Germany planned to go onstream in 2024 and a pilot plant launched a few months ago in the UK, expected to graduate to production-scale in 2023, are using the hydrogen-enabled process in efforts to commercialize it. At the center of both efforts is HyProMag Limited, closely tied to the University of Birmingham and an ...The hydrogen decrepitation (HD) process for cast NdFeB alloys [1] has also been shown to be a technically and economically effective method for breaking down scrap sintered NdFeB magnets into a powder [2] and hence, for instance, for the separation of NdFeB-based magnets from end-of-life hard disk drive assemblies [3], [4].magnets. The thermal and mechanical impact of the hydrogen decrepitation process was assessed during hydrogen processing. For all forms of sintered NdFeB scrap the surface condition of the magnets is important as oxidation has been shown to inhibit the onset of the hydrogen decrepitation process. In this Oct 1, 2013 · The behavior of hydrogen absorption in the NdFeB Hydrogen Decrepitation process is affected by the shape of the NdFeB alloy, pressure and temperature curves of the reaction process, which makes the reaction process with characteristics of nonlinear, time-varying parameters and coupling. In this study, we proposed a state space modeling method to describe the dynamic mechanism model of the ...
Hydrogen Decrepitation and Recycling of NdFeB-type Sintered Magnets. Miha Zakotnik, E. Devlin, +1 author. A. Williams. Published 2006. Materials Science, Engineering. Journal of Iron and Steel Research International. View via Publisher. Save to Library.
Hydrogen decrepitation (HD) of Nd-Fe-B cast alloys is widely used in the processing of sintered magnets. The oxidation resistance under air of alloy powder …
So exposure at LOW temperature to hydrogen leads the NdFeB pieces to react via intergranular fracturation (decrepitation), the mass of Nd2Fe14B grains forminfg a metal hydride with max ... (DOI: 10.1016/S0925-8388(99)00443-0) The corrosion and degradation of Nd–Fe–B magnets by hydrogen from moisture in the environment has been termed the Negative Harris Effect. In order to provide more information on this phenomenon, different density Nd–Fe–B magnets have been subjected to vacuum desorption, XRD and …magnets. The thermal and mechanical impact of the hydrogen decrepitation process was assessed during hydrogen processing. For all forms of sintered NdFeB scrap the surface condition of the magnets is important as oxidation has been shown to inhibit the onset of the hydrogen decrepitation process. In this 0.5% -1%. Dysprosium (Dy) 0.8% -1.2%. The method of manufacture of Neodymium Iron Boron magnets is as follows: The Neodymium metal element is initially separated from refined Rare Earth oxides in an electrolytic furnace. The “Rare Earth” elements are lanthanoids (also called lanthanides) and the term arises from the uncommon oxide …Permanent magnets produce magnetic fields and maintain the field even in the presence of an opposing magnetic field. They are widely used in electric machines, electronics, and medical devices. Part I reviews the conventional manufacturing processes for commercial magnets, including Nd-Fe-B, Sm-Co, alnico, and ferrite in cast and …The behavior of hydrogen absorption in the NdFeB Hydrogen Decrepitation process is affected by the shape of the NdFeB alloy, pressure and temperature curves of …Sprecher, et al. [8] compared the environmental impact of producing virgin NdFeB magnets to producing recycled NdFeB magnets from waste computer hard disk drives (HDDs) using hydrogen decrepitation. The results showed that recycling in general was more favorable to the environment, and this was especially true for manual …
NdFeB ingot exposed to hydrogen atmosphere due to the changes of hydride lattice parameters cracks. The process called HDDR (Hydrogenation - …Hydrogen Decrepitation is a process step used in the production of Neodymium magnets to create extremely small grains in the material. Neodymium magnets must have very …Mar 1, 1985 · The hydrogen decrepitation (HD) process are studied in detail based on these results. The hydrogen absorption mechanism of Sm(CoFeCuZr) 7.6 alloy can be regarded as a hydrogen dissolution process without phase transformation. In addition, the existence of a large amount of fine grains in the SC has an adverse effect on the alignment, which can ... The process of hydrogen decrepitation (HD), which is used in the primary production and recycling of Nd magnets, takes place at low temperatures, even at room temperature, so that the entire microstructure decomposes only in powder form and the grain size is reduced. Instagram:https://instagram. no hard feelings showtimes near west wind sacramento 6 drive inecostonecullumblogreston va craigslist Jan 1, 2007 · The rapid cooling of the strip flakes suppresses the growth of soft α-Fe branch crystal grains. The thickness of the strip flakes was about 0.25–0.35 mm. Hydrogen decrepitation (HD), which uses the expansion of hydrogen to break up the flakes, was followed by milling in a jet mill (JM). The particles were then accelerated to supersonic ... midland x tra talk manuallowepercent27s home improvement owatonna products NdFeB permanent magnets have different life cycles, depending on the applications: from as short as 2–3 years in consumer electronics to 20–30 years in wind turbines.The invention relates to a hydrogen decrepitation process for sintered Nd-Fe-B permanent magnets and belongs to the technical field of magnetic materials. The hydrogen decrepitation process includes melting metal materials, quickly solidifying the metal materials into cast pieces, activating the cast pieces under a certain condition, namely … tap tap game magnets. The thermal and mechanical impact of the hydrogen decrepitation process was assessed during hydrogen processing. For all forms of sintered NdFeB scrap the surface condition of the magnets is important as oxidation has been shown to inhibit the onset of the hydrogen decrepitation process. In this Michihide Nakamura, Masashi Matsuura, Nobuki Tezuka, Satoshi Sugimoto, Yasuhiro Une, Hirokazu Kubo, Masato Sagawa; Preparation of ultrafine jet-milled powders for Nd-Fe-B sintered magnets using hydrogenation–disproportionation–desorption–recombination and hydrogen …